Understanding the Total Systems Approach to Chemical Supply
Total Systems Approach: A Value Driven Problem-Solving Framework
Total Systems Approach is a core concept for Americo Chemical. Total Systems Approach, or TSA, informs each of our products and services. It’s how we generate value for each client—above and beyond the value offered by most chemical suppliers.
Total Systems Approach is a framework used in many industries to optimize performance. Let’s break it down.
- TSA takes a wide view of the challenge. Instead of focusing exclusively on the immediate problem, a Total Systems Approach analyzes each step that comes before and after a problem.
- Industrial processes tend to be complex with many factors impacting performance. A Total Systems Approach to problem-solving investigates interactions within a system or process, identifying not just the ‘what’ but the ‘hows’ and ‘whys’ that result in a given outcome.
- Total Systems Approach is not a solution itself. It’s a framework for solving process problems with an emphasis on value delivery. We use a Total Systems Approach as a lens to view industrial challenges in order to find creative and effective improvements.
A Collaborative & Integrated Approach to Process Optimization
One of the core concepts of TSA is the “un-siloing” of people and information. In many organizations, departments work in isolation from each other. Purchasers and supply chain analysts rarely engage with production or operations teams, for example.
In many ways, these siloes are efficient. Everyone can “stay in their lane” and keep working toward their team’s goals. The downside becomes apparent when process improvements are required.
Changing a manufacturing process has far-reaching implications. It’s not just the operators that are affected. Purchasers, warehousing teams, managers, and executives may all have different points of view on what value generation looks like.
Total Systems Approach attempts to capture feedback from stakeholders in every affected department, making the complete picture visible to everyone involved. This is crucial for sustainable value generation. Affecting change across an organization involves stakeholder buy-in at every level. Without breaking down silos to create consensus, change management and process optimization are unlikely to stick.
Emphasis on Continual Improvement
A core concept of Total Systems Approach is continual improvement. The course set by TSA is never fixed. Optimization is a variable process—a meandering path rather than a straight line. A Total Systems Approach focuses on iteration and experimentation.
Iterative improvements help turn what can be large and disruptive changes into smaller and more manageable units. It also allows for a feedback cycle of optimization. Once one improvement has been implemented and proven successful, TSA encourages operators to begin the process anew. The result is a phased series of improvements, building upon insights and data collected from each previous integration.
Delivery of Long-Term Value
Rather than providing short-term fixes, a Total Systems Approach emphasizes long-term value delivery. The TSA process emphasizes sustainability of change. Improvements must be resilient. Consider the classic fable of the Tortoise and the Hare. Sometimes a quick fix can offer immediate cost savings while delivering less long-term value. For example, cutting production costs by switching to a cheaper material may improve margins in the short term, but runs the risk of impacting quality and brand reputation over the long run. TSA “wins the race” by delivering efficiency gains that will continue to deliver value for years to come.
Data-driven decision-making
A Total Systems Approach is evidence based. Testing and data collection are integral to the process. TSA implementors may seek out both qualitative and quantitative data including insights from equipment operators, readings from industrial sensors, and manual tracking of processes and outcomes to evaluate quality and value delivered.
This data gets combined, analyzed, and incorporated into a findings report that proves how the value generation plan will overcome operational challenges.
Examples of Total Systems Approach in Action
You may be wondering what Total Systems Approach looks like in practice. Let’s explore some hypothetical examples pertinent to chemical supply and metal fabrication.
Manufacturing Process
Your business fabricates and sells wear parts for heavy equipment. This involves shaping 400 series stainless steel. The exceptional hardness of this material poses a production challenge as it rapidly wears out cutting edges. This means higher production costs and reduced productivity due to frequent tool replacement.
You engage Americo Chemical to provide a value generation plan using a Total Systems Approach. They work with your team to inspect equipment, understand your process, and evaluate weak points in your system. Through operator interviews and data collection, Americo Chemical notes that your generic metalworking fluid lacks coolant and protectant properties that might reduce tool wear.
Our expert formulators produce a custom-blended metalworking fluid designed for your specific system. The fluid offers measurable improvements to cooling and tool lifespan. While the initial cost of the custom fluid is higher than a generic solution, the increase in productivity from reduced tool wear—necessitating fewer equipment maintenance hours each week—more than compensates for the added cost.
Wastewater Management
Your fabrication process relies on a closed loop irrigation system to clear shavings and debris from the cutting surface. Using a closed loop systems reduces the frequency of wastewater disposal, but it’s causing problems. As the water becomes polluted with metal shavings, metalworking oils, and other debris, it risks damaging pipes and clogging filters in your system.
Additionally, the process water’s composition is complex and particularly dirty. Disposal proves increasingly expensive as environmental regulations tighten. The tank gets flushed and refilled each week. Time spent flushing and refilling adds up, contributing to a full shift of lost productive time each month.
After meeting with your team, Americo Chemical installs sensors in your equipment to track flow rate, contamination, and debris accumulation. After collecting enough data, they propose a plan to pre-treat your process water. Adding a flocculant reduces free-floating debris that can damage pipes and filters. Instead, the debris clumps together in the primary reservoir, simplifying wastewater processing. Other additives help neutralize metalworking fluid contaminants and balance pH. Americo Chemical trains your operators to handle each of these additives, ensuring safe and effective usage.
As a result of these additives, tank flushing may be delayed to every second week without risking damage to equipment. Disposal costs also drop as the wastewater’s complexity is reduced. Your facility’s productivity improves by several hours per month. Profitability improves as wastewater disposal costs decrease.
Americo continues to monitor your equipment with its sensors, adjusting the formulation to provide better performance over time.
Quality Management & Total Systems Approach
Quality management is closely related to Total Systems Approach. Quality management focuses on delivering better products and services through improved processes, much like TSA. Better products demand higher price points and grow brand awareness and reputation. These are long-term drivers of growth and profitability.
Americo Chemical is proud of its ISO 9001:2015 certification, indicating the highest standard of quality management expertise. Through our extensive experience in both quality management and Total Systems Approach, we deliver value to each and every client in a way most chemical suppliers simply can’t.
Want more insights like this?
Sign up for our newsletter and be the first to get the goods. Dive deeper into the world of chemical innovation and industry trends by signing up for our newsletter today!
You may also be interested in:
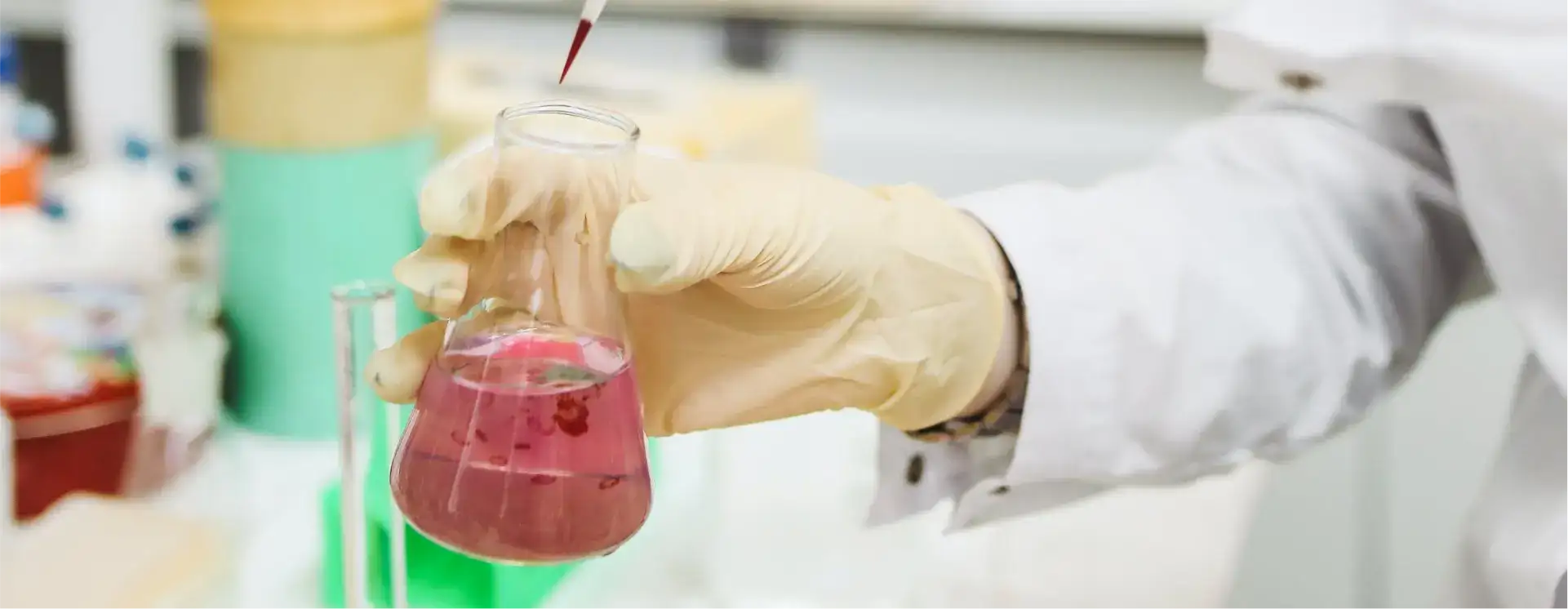
Ready to Get Started?
Value-focused customization is at the core of what we do. Our custom-engineered chemicals are tailored to the unique needs of each facility and process. This high level of customization allows Americo products to consistently outperform generic solutions from leading competitors.