Sustainability in Chemical Manufacturing
Sustainability in chemical manufacturing is an often-overlooked way that our society can reduce its environmental impact without sacrificing quality of life or economic viability. Did you know that the chemical sector is the most energy-hungry industrial sector, and the third-highest carbon emitting industry in the United States?
Sustainability isn’t optional anymore. Nearly every sector has found itself impacted by tightened regulations and customer expectations for sustainability.
In the United States, legal sustainability requirements have grown increasingly stringent over the past twenty years. Maintaining competitiveness with less regulated international markets while meeting ecological commitments is an added challenge for American manufacturers.
An economic case for sustainable chemicals?
It’s not all bad news for your bottom line. A commitment to sustainability comes with perks like access to certifications and memberships that keep you informed while promoting your brand. Manufacturers who go above and beyond to reduce their environmental footprint can become certified B-corps. They may choose to join sustainable trade associations, gaining access to industry insights and facilitating partnerships with like-minded businesses. Over the long term, adopting a sustainable chemical process will save money through reduced waste management fees and lowered risk of fees and fines from polluting activities.
The best benefit provided by sustainable chemistry is its positive impact on our communities. Every American deserves to live and work in safe and healthy communities. Sustainable chemical manufacturing results in less hazardous waste, typically requires less energy, and produces fewer secondary pollutants and emissions than conventional processes. These benefits add up to improve the environmental health and integrity of communities across America and around the world.
Let’s look at how sustainability in the chemical sector has evolved over the years, where it’s at now, and how your manufacturing processes can be made cleaner—and in some cases, cheaper and more effective—by embracing a sustainability-first focus.
Environmental history of chemical manufacturing
Through much of the twentieth century, American environmental policy concerning chemical manufacturing could be characterized as lax, non-specific, and incomplete. Until the passage of legislation like the Clean Air and Clean Water Acts between 1970 and 1972, industrial regulation consisted of patchwork local and municipal laws. In many cases, the pre-1970s laws were toothless, vague, or otherwise ineffective at curbing bad behavior.
As a result, many 20th century chemical manufacturers took the path of least resistance. Companies disposed of waste by burying it, dumping it into waterways, or simply allowing waste streams to flow to ground unabated.
This resulted in a number of infamous environmental disasters including the Love Canal incident in New York. The Hooker Chemical Company used the Love Canal region as a dumping ground for a variety of hazardous waste materials before selling the land. Over the next two decades, a school and neighborhood were established in the area. Residents experienced extremely high rates of cancer, birth defects, and poor health as a result of severe chemical contamination of soil and groundwater.
It took about twenty years before concerns about health issues in Love Canal got taken seriously. By the late 1970s, the region was evacuated. It took until the passage of the 1980 Comprehensive Environmental Response, Compensation, and Liability Act for the federal government to begin remediation—a process that would continue until 2004 and involve the demolition of hundreds of houses and the permanent evacuation of over 900 residents.
Today’s regulatory framework for sustainable chemistry
Decades of legislative expansion and refinement have resulted in a more comprehensive framework for managing environmental issues in the chemical sector.
In the years following the Love Canal incident, the US federal government expanded upon existing environmental regulations, for instance by introducing the 1980 “Superfund” program. Superfund taxes oil and gas and chemical companies, maintaining a reserve fund used to clean up waste sites, spills, and environmental disasters caused by industry.
Further expansion of regulations through the 80s and 90s include modernization of clean air laws and expanded disclosure requirements for polluting industries.
Through the 2000s, US environmental laws became more stringent with an emphasis on harmonization with regulations in major export markets.
Today, the philosophy surrounding pollution and waste management is quite different from how these issues were approached in the ‘70s. An increasing focus on environmental and restorative justice attempts to rectify historical wrongs committed by polluting companies against marginalized communities. In a more general sense, regulations have shifted from addressing the outcomes of polluting industry to addressing pollution at the source—intervening during the polluting process rather than merely prescribing cleaner ways to deal with the resultant waste.
Technology and sustainability: advancements in chemical manufacturing
While increased scrutiny and more meaningful regulation contribute greatly to a cleaner and greener chemical sector, technological advancements are at least as important.
For instance, one of the world’s most used and most essential chemicals is ammonia. Without it, modern agriculture is impossible. Most ammonia is produced through the so-called “Haber-Bosch process.” Ammonia consists of nitrogen and hydrogen. Nitrogen is freely available in the air we breathe. Hydrogen is trickier to come by. Conventionally, it’s extracted from methane gas using steam—an energy intensive process.
Using a catalyst like iron, nitrogen and hydrogen gases get compressed and heated to high temperatures. This results in the production of ammonia gas, which gets cooled and extracted as a liquid.
Earlier, we mentioned that the chemical industry is the single biggest energy consumer of energy worldwide. Ammonia production is the most energy-hungry process in the chemical industry, requiring about 1% of the world’s energy and producing about 1% of the industrial world’s carbon emissions.
Through technological innovation, that massive energy consumption is dropping. Over the past fifty years, process improvements ranging from advanced heat exchangers that reduce energy waste to greener sources of hydrogen and upscaling of ammonia production facilities have dropped energy usage per ton of ammonia produced by up to 40%. This is an example of process intensification (PI) where a range of process optimizations combine to result in a large efficiency gain.
Other technologies impacting chemical sustainability
Chemical recycling
For the most part, the chemical industry has always prioritized re-using and efficiently managing reagents when possible. There’s no sense in disposing of a process chemical if it can be cleaned up and re-used or repurposed elsewhere.
Modern methods of chemical recycling allow for even more significant re-use of chemicals. New technologies allow companies to break complex plastics back down into monomers, allowing waste materials to be remade into virgin plastics.
This is promising new technology, though recycling often proves to be energy intensive. Bringing down energy requirements and reducing the process’ cost will make it more viable for manufacturers in the near future.
Biological chemical manufacturing processes
One exciting area of innovation in the chemical world is the increasing use of bioengineered organisms to facilitate chemical manufacturing. Imagine a bacteria that eats a feedstock chemical and excretes an end product. This is an emerging reality!
Many companies now specialize in the production of yeast, bacteria, or enzymes that produce useful chemical products. For example, there’s an engineered strain of bacteria that eats methane and excretes materials used in the production of bioplastics. Some engineered microbes can produce natural flavor and fragrance compounds from readily available feedstock, reducing the need for carbon-intensive agriculture in producing and extracting such compounds.
CCUS (Carbon capture, usage, and storage)
Carbon capture is an increasingly familiar technology found in many industries. The idea is to prevent CO2 and other greenhouse gases from venting to the atmosphere. By capturing and sequestering such pollutants, industries can lower their emissions without fundamentally altering their process.
In many cases, stored carbon can be repurposed for other processes. CO2 is a critical reagent for many important products and chemicals. It can be used in plastics production, the creation of biofuels, or to create or improve construction materials.
Solar chemical processes
There’s no cleaner source of energy than the sun. We use the sun’s energy directly or indirectly in all kinds of ways. After all, what are fossil fuels but ancient plants and animals turned into hydrocarbons? In this sense, they are storing energy from hundred-million-year-old sunlight.
An example of a solar chemical process is the photolysis of water into hydrogen and oxygen. As previously described, important chemical processes like ammonia production rely on hydrogen gas. Solar processes facilitate a low carbon means of splitting water into its atomic components, separating and storing the gases for use in other processes. While the process has its challenges—it can be slow, expensive to deploy, and expensive to scale—it’s a powerful way to reduce energy requirements for major industrial processes.
Economic benefits of sustainable chemical manufacturing
Sustainable chemistry offers myriad benefits to our communities and our planet. How does it impact the bottom line for companies that choose sustainable options?
While the up-front costs for sustainable chemicals remain higher than for conventional options in most cases, the long-term view is different. Whether through risk management or access to new business opportunities, a case may be made that sustainable chemicals benefit manufacturers in the short and long term.
Access to funding and partnerships
As businesses face increasing scrutiny regarding their environmental record and commitments, those who fail to meet expectations may experience direct and indirect penalties. For instance, many public procurement processes now score applicants on their social and environmental record. Making meaningful commitments to sustainability, like maintaining membership in good standing with environmental groups, can help businesses close more contracts. Some of these groups and associations may present new business opportunities through networking with like-minded partners.
In other cases, a commitment to sustainable practices can open doors to grants and funding. Funding may even be acquired to help hasten the transition to sustainable technology.
Enhanced worker safety
Keeping workers safe and healthy keeps them productive. Many sustainable options are also safer and gentler to work with. Companies dedicated to maintaining a safe workplace should audit their chemical usage to ensure that safe and eco-friendly options get prioritized.
Risk management
Remember the Love Canal incident we discussed earlier? It’s one of many environmental disasters in the United States. While there are examples of companies “getting away with it,” these disasters can have massive legal and financial consequences for the businesses held responsible. Even in cases where a safer or more sustainable chemical is more expensive without otherwise adding value to the process, if it contributes to reduced legal exposure it may be a good idea to view it as insurance against future problems.
Barriers preventing adoption of sustainable chemistry
Across America, more and more companies choose sustainable options. They make this choice for a variety of reasons. Government regulations and financial incentives offer a carrot-and-stick model for adopting sustainable tech. Companies may choose to go green as way to differentiate themselves in the market. Some companies may choose sustainable options for moral reasons.
Nonetheless, there remain barriers that prevent wider-spread adoption of sustainable chemicals.
Supply chain management
Because sustainable manufacturing processes tend to be more complex or time-consuming than conventional options, companies may have concerns about supply chain. As sustainable options eat up more market share versus conventional products, we should see an increase in production and supply that will put manufacturers at ease.
Process adjustments
Many sustainable products are drop-in solutions. Sustainable ammonia is identical to conventionally manufactured ammonia. In some cases, more sustainable chemicals have different chemical properties than the conventional chemical they replace. A need to swap out tooling or otherwise modify a process is a strong disincentive for many manufacturers. Finding the time to make the swap, train staff on a new process, and still meet manufacturing commitments can be difficult.
High upfront costs
Today’s economy is tight, with high interest rates and low capital reserves encouraging businesses across America to carefully manage their spending.
In this context, it’s hard to ask manufacturers to pay more up-front for essential chemicals. Addressing the cost disparity between sustainable and conventional chemicals is a major challenge without a single answer. A combination of subsidies, regulatory pressure, and market pressure (customer demand for more sustainable products) will help close the gap over time.
Conclusion
In conclusion, as we face the pressing challenges of climate change and environmental degradation, the chemical manufacturing sector stands at a pivotal junction. Embracing sustainability is not merely an ethical choice but a strategic imperative that promises significant benefits across economic, environmental, and social dimensions. Companies that pivot towards sustainable practices are poised not only to comply with increasingly stringent regulations but also to enhance their market competitiveness through innovation and improved public perception.
As technology continues to evolve and market dynamics shift towards green solutions, the adoption of sustainable practices in chemical manufacturing is not just a forward-thinking strategy—it is an inevitable and essential transition that will define the future of the industry.
Want more insights like this?
Sign up for our newsletter and be the first to get the goods. Dive deeper into the world of chemical innovation and industry trends by signing up for our newsletter today!
You may also be interested in:
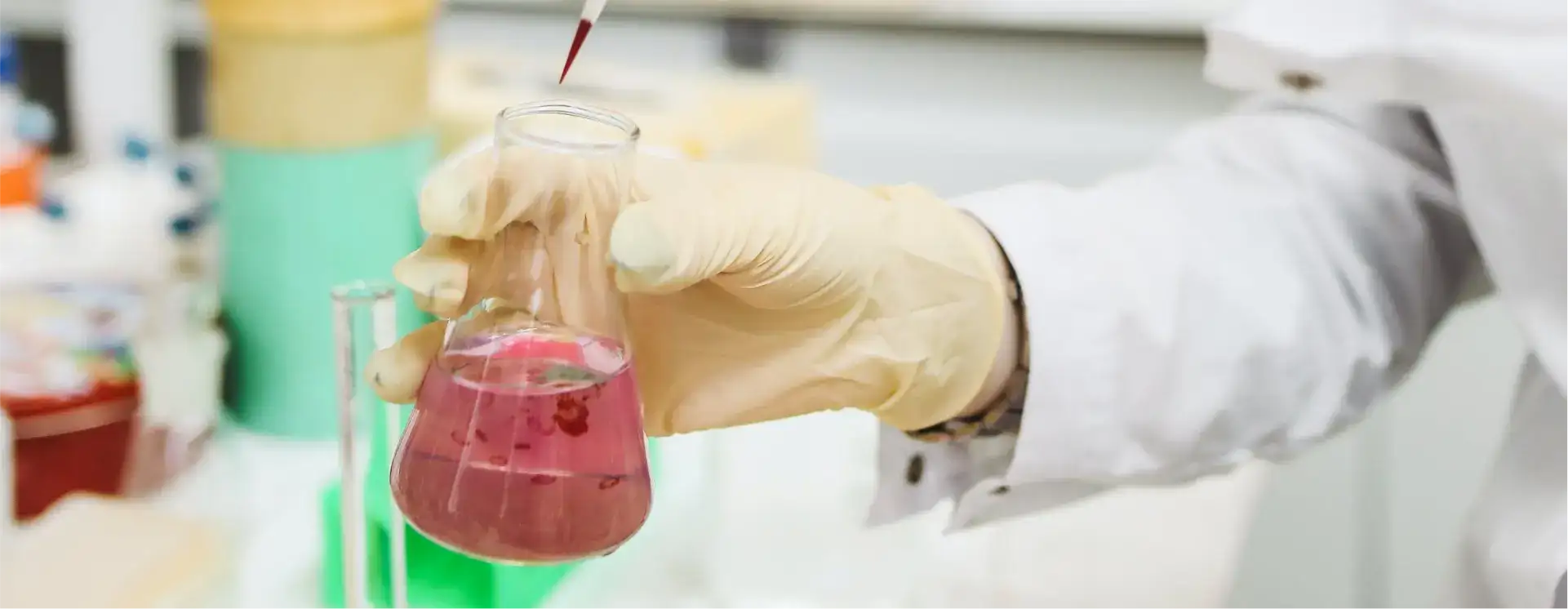
Ready to Get Started?
Value-focused customization is at the core of what we do. Our custom-engineered chemicals are tailored to the unique needs of each facility and process. This high level of customization allows Americo products to consistently outperform generic solutions from leading competitors.