Eliminating Hazardous Air Pollutants and VOCs in Manufacturing
Air pollution is a critical concern for manufacturers of all types. Hazardous air pollutants (HAPs) are a class of compounds defined by the United States government, spanning nearly two hundred distinct types. Though not all are created equally—pollutants like benzene are considerably more hazardous to humans than solvents like methanol—limiting the production and release of HAPs is socially, environmentally, and economically responsible. Even relatively harmless air pollution can result in unpleasant odors and irritation among sensitive community members.
Many forms of pollution remediation focus on upstream and downstream factors rather than the manufacturing process itself. There are effective process adjustments that may be made to either capture or destroy pollutants before they impact your workers, facility, or community at large.
Clean Air Act and Hazardous Air Pollutants
Since 1990, the American Environmental Protection Agency has maintained a list of regulated hazardous air pollutants. The list’s composition has changed over time, currently containing 188 distinct materials ranging from asbestos to vinyl acetate. Industries that work with these pollutants must adhere to higher standards of regulatory compliance. This includes monitoring and reporting activity, installation of effective filtration and recapture devices, and implementation of strict health and safety standards when handling regulated substances.
Hazardous Air Pollution in Manufacturing
In manufacturing, VOCs and PFAS are common hazardous air pollutants, though many facilities have begun to phase out PFAS. Broadly speaking, there are two types of remediation for air pollutants: capture and control. Capture involves preventing the release of air pollutants through filtration systems and chemical intervention. Control involves destroying or neutralizing the pollutants through a variety of methods.
Measuring capture/control of hazardous air pollutants
In order to measure improvements in air pollution footprint, a facility must first establish a benchmark. Implementing Continuous Emission Monitoring Systems (CEMS) is a logical first step to reducing HAP emissions.
These systems involve several components that help measure both specific pollutants and overall physical complexion of exhaust. For instance, gas analyzers may be tuned to identify and measure specific pollutants like VOCs, while more general sensors may analyze flow rate, temperature, opacity, and moisture content to provide a more general view of the exhaust’s composition.
Methods of capture
Absorption
Absorption relies on chemical reactivity to capture pollutants before they vent to atmosphere. One example would be forcing exhaust gases through a chamber filled with a reactive liquid that removes specific pollutants. For instance, an acidic solution can remove ammonia from exhaust gases. The removed ammonia can be safely disposed of or extracted and re-used in other processes if it’s economically feasible to do so.
Adsorption
Adsorption captures pollutants on the surface of a material like activated carbon. A bed of activated carbon can attract and capture pollutants like VOCs. In most cases, VOCs can be recovered through thermal or steam regeneration, replenishing the adsorbent potential of the carbon while recapturing the pollutant for re-use or destruction.
Condensation
Another simple form of pollution capture is condensation. Hot exhaust can run through a cooling system, causing certain pollutants to condense into a liquid for recapture. This works for certain types of pollutants but won’t work for others whose dewpoint is too low to make condensation feasible.
Methods of control
Chemical Scrubbing
Chemical scrubbing uses reagents to convert a hazardous pollutant to a more manageable form. It’s similar to absorption but focused on disposal rather than recapture. For instance, a sodium hydroxide scrubber can convert dangerous chlorine into relatively safe chloride. This makes management and disposal safer and less costly.
Flaring
Perhaps the simplest method of control, flaring refers to burning off harmful pollutants. Depending on the efficiency of combustion, this can greatly reduce the harmfulness of certain pollutants. Compared to other methods, it’s less clean but relatively easy and reliable to implement in relevant processes.
Catalytic Oxidation
Many pollutants like VOCs react with catalysts at high temperatures, degrading into their base components: easily managed materials like water and CO2. The process involves pre-heating gases before feeding them into a catalytic converter, usually using a metal like platinum as a catalyst. The gas reacts with the catalyst to generate heat, water, and CO2. After cooling and further filtration, the relatively clean exhaust gas is vented to atmosphere. Catalytic oxidation can be an energy efficient option for cleaning up exhaust gas as the process can sustain itself through heat generated by the reaction. The process does have downsides such as the catalyst’s susceptibility to fouling, which results in degraded performance.
Conclusion
As we’ve seen, managing air quality isn’t just about compliance—it’s about taking proactive steps to ensure the health of your employees, the environment, and the community. With advanced methods available to capture and control hazardous air pollutants and VOCs, now is the time to assess and enhance your existing systems.
Whether you’re looking to install a new system or upgrade your existing infrastructure, consider working with Americo Chemical to conduct a comprehensive audit of your current pollution control technologies. By monitoring, analyzing, and addressing your pollution footprint, you can protect your business from costly fines while doing better by your workers, customers, and local community.
Want more insights like this?
Sign up for our newsletter and be the first to get the goods. Dive deeper into the world of chemical innovation and industry trends by signing up for our newsletter today!
You may also be interested in:
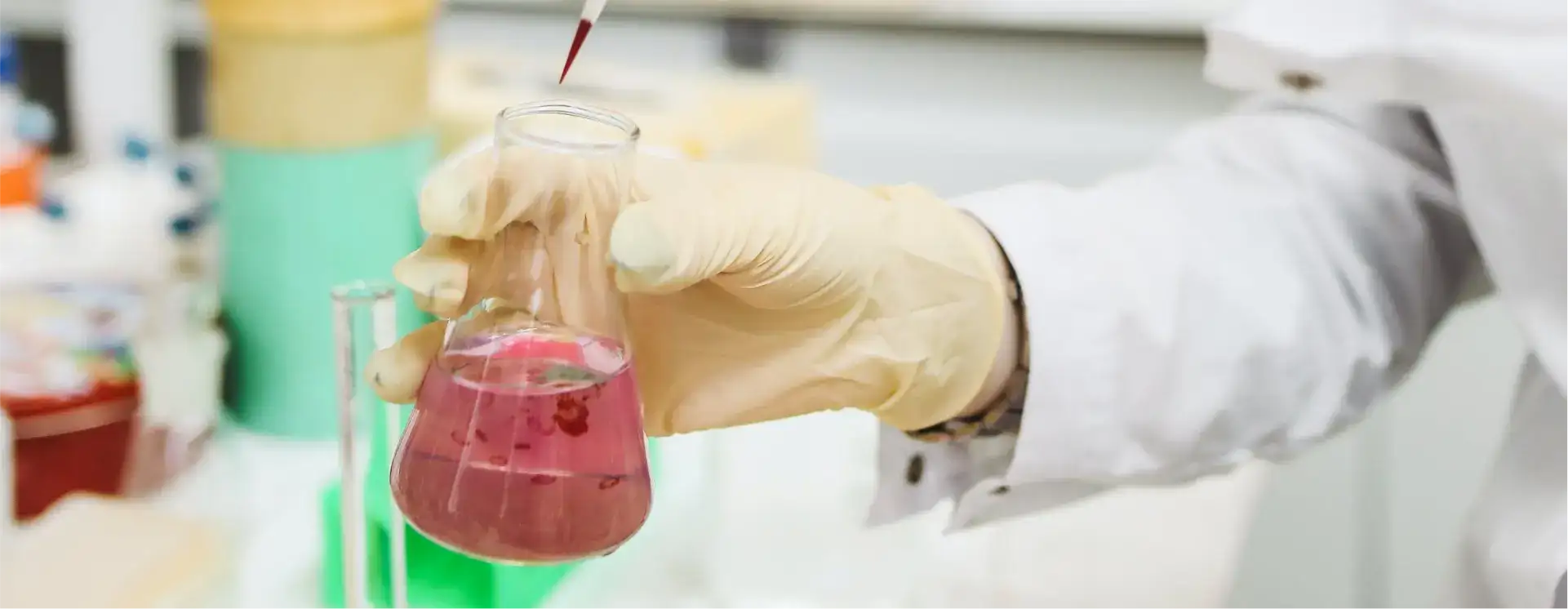
Ready to Get Started?
Value-focused customization is at the core of what we do. Our custom-engineered chemicals are tailored to the unique needs of each facility and process. This high level of customization allows Americo products to consistently outperform generic solutions from leading competitors.