Reducing energy consumption in the manufacturing sector through tailored chemistry
When manufacturers explore options to reduce energy consumption, things like high efficiency equipment and stricter energy use policies come to mind. These are important techniques in decreasing energy usage, but they are not the only techniques. Addressing high energy usage through process chemistry is an important consideration for any energy optimization strategy. Let’s explore the regulatory context spurring energy optimization initiatives throughout the United States before demonstrating several ways that superior chemistry can result in energy savings.
Energy usage in manufacturing and industry
In 2022, industrial activity accounted for 33% of all energy consumption in the United States. 76% of energy usage in the industrial sector is the result of manufacturing activity, meaning that manufacturing consumes about 25% of all energy in the United States each year.
Chemical manufacturing is the most energy-hungry segment of the manufacturing sector, accounting for 37% of manufacturing energy consumption. This number may be slightly misleading on its face; 60% of energy consumption in the chemical manufacturing sector is through non-fuel applications. For example, natural gas is a crucial feedstock for the production of chemical fertilizers. This gas isn’t burned for heat or electrical power, but still gets measured as consumed energy by the EIA.
Given the scale of energy usage in manufacturing, particularly in chemical manufacturing, it makes sense to focus on chemical processes as a means to reduce energy consumption and meet stringent emissions targets set by the U.S. government such as net zero carbon emissions by 2050.
Start with a process audit
In order to optimize your energy usage, you must first understand your energy usage profile. This involves installing and monitoring metering systems, identifying low-hanging fruit for energy usage reduction, and other planning and analysis activities. Americo Chemical’s quality management expertise make us a great partner for getting started with process auditing and energy management.
Chemical solutions to energy problems
Superior chemical supply can reduce energy footprint at your facility in a few ways. Using chemicals whose production process is less energy intensive reduces upstream energy usage. Chemicals that provide similar benefits at lower process temperatures—or that last considerably longer than alternatives—can decrease energy consumption. Chemicals that improve equipment performance or extend equipment lifespan can also improve energy efficiency.
Green Chemistry
Green chemistry can mean a lot of things. Some green chemicals are biodegradable or less environmentally harmful, requiring less recovery or neutralization before disposal. This can have both direct and indirect impacts on energy usage. Consider a chemical solution that requires less heat to decompose into something safe for disposal. The actual process of disposal becomes less energy intensive. Simplified disposal processes are easier and often require less manpower and energy usage.
Green chemicals also include those which are produced with less energy intensive methods. For instance, ammonia production accounts for about 2% of global energy demand alone! Green ammonia is a focus area for the chemical manufacturing industry, with plans to use excess renewable energy during off-peak hours to cut the emissions profile of ammonia production.
Bio-based and enzymatic chemistry
An exciting and emerging development in sustainable chemistry is the introduction of bio-based and enzymatic solutions for manufacturers. Though these emerging technologies may not be ready for prime time yet—both are susceptible to higher costs and difficulty scaling production—they may soon offer drop-in replacements for energy intensive and polluting chemistry across the manufacturing sector.
Bio-based chemicals attempt to replace petroleum-based solvents and coatings with chemicals derived from feedstock like corn, algae, or oilseed crops. The idea is that, in conjunction with more energy efficient farming practices, these feedstocks are less polluting and more renewable than conventional chemicals.
Enzymatic catalysts offer benefits such as lower process temperatures and improved safety for workers. They suffer from the same downsides as other bio-based chemicals: higher costs and lower availability. As this technology continues to improve, it may become a disruptive force in process chemistry.
Implementing an energy-smart culture
Chemical interventions can reduce energy usage, but only with buy-in from workers and management. In order to achieve the greatest energy savings, businesses must foster an energy-smart culture. Implementing this may require taking actions such as:
- Establishing energy usage benchmarks and realistic but ambitious and measurable goals.
- Creating clear policies and objectives, including new routines and requirements aimed at reducing energy consumption
- Providing workplace incentives for reduced energy usage
- Leading by example, ensuring managers and supervisors “walk the walk”
Conclusion
As the manufacturing sector grapples with the dual challenges of high energy consumption and increasing regulatory pressure to reduce environmental footprints, the pathway forward requires a multipronged strategy. From rigorous process audits to the adoption of green chemistry and bio-based solutions, there are many methods to tackle the issue. Americo Chemical can be your partner in achieving energy savings through process enhancement and custom chemical solutions.
Want more insights like this?
Sign up for our newsletter and be the first to get the goods. Dive deeper into the world of chemical innovation and industry trends by signing up for our newsletter today!
You may also be interested in:
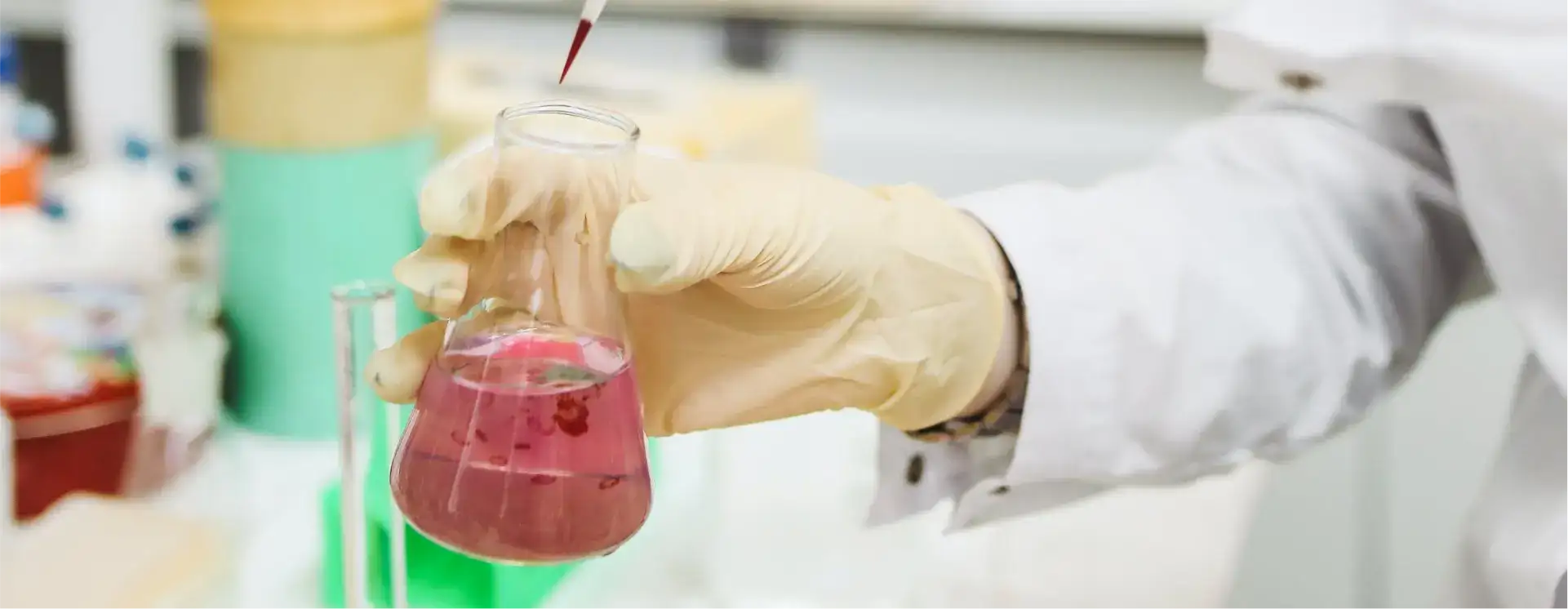
Ready to Get Started?
Value-focused customization is at the core of what we do. Our custom-engineered chemicals are tailored to the unique needs of each facility and process. This high level of customization allows Americo products to consistently outperform generic solutions from leading competitors.