Process methods for improving manufacturing sustainability
Climate change and pollution pose direct challenges to the viability and profitability of manufacturers worldwide. The recent supply chain woes caused by the COVID-19 pandemic and ongoing geopolitical events demonstrate how upstream challenges including extreme weather can severely impact downstream manufacturers. Microsoft’s sustainability report for executives highlights $54bn in insured losses in the manufacturing sector in 2020 due to “secondary perils.” These perils include extreme storms, flooding, and forest fires. Up to 60% of all insured losses in the sector resulted from this category. Such challenges are anticipated to increase through the next century and beyond.
Despite this, manufacturers lag behind other industries when it comes to thinking and talking about sustainable practices. When manufacturers do think about sustainability, they tend to focus on innovative new materials, potentially ignoring opportunities to optimize their processes.
No amount of sustainable practice will undo the effects of climate change, but they can contribute to lower operating costs, more efficient processes, and more competitive products in a market increasingly sensitive to social good value adds.
Americo Chemical specializes in providing beginning-to-end solutions for physical and chemical processes in manufacturing. Our Total Systems Approach considers product quality, total productivity, cost-effectiveness, and sustainability in equal measure. Let’s explore how Americo Chemical approaches sustainable manufacturing.
What do we mean by “sustainable?”
When you hear the word “sustainable,” your first thought is probably something about the environment. This is the most common way to use the word in a business context, but sustainability extends beyond just the environment. There are also social and economic contexts for sustainability.
For example, changing market conditions including more costly labour and materials can make an otherwise-profitable business unsustainable to operate. Bad workplace culture or poor compensation can make a business socially unsustainable, as its core workforce may leave for better opportunities.
Americo considers sustainability across all three of these dimensions: environmental, economic, and social. Let’s explore how Americo Chemical implements sustainability in its own practices, as well as ways we help clients improve their own sustainability.
Americo’s sustainability commitment
Zero discharge facility
Americo’s production facility is Zero Liquid Discharge (ZLD) compliant. This means that during production, no wastewater gets discharged to the environment. Waste materials are collected and handled appropriately. Where possible, water and other materials get cleaned and re-used in other processes.
PFAS-free products
PFAS substances are a group of chemicals used in a range of coatings and surface treatments. These chemicals—of which there are millions—typically provide non-stick, water resistant, and stain resistant properties to products. Think of Chemours’ well-known Teflon anti-stick pans. That’s PFAS in action.
While PFAS substances are useful, they’re also harmful to people and the environment. They are so-called “forever chemicals” that don’t break down naturally in the environment. Instead, they persist in ecosystems and even within organisms—humans included—contributing to a range of chronic health conditions including breast and testicular cancer, low fertility rates in men, and various hormonal disruptions.
PFAS and other forever chemicals are targets for regulation and restriction. Recently, the EPA set an official limit on PFAS levels in drinking water. Companies like 3M have made commitments to cease PFAS production by 2025.
Americo is a PFAS-free facility. We have elected not to offer PFAS products as part of our commitment to reducing our environmental footprint.
Input and output analysis
Americo operates its own business with the same quality management techniques we apply to each client. By understanding our manufacturing inputs, outputs, and processes inside and out, we’re continually working to improve our efficiency, safety, and environmental sustainability.
Commitment to long-term employee satisfaction
We’re proud of the number of long-term full-time employees at Americo. Superior processes are core to our offering. Maintaining a healthy, safe, and happy workforce who know our methodology and can effectively execute our processes ensures customer satisfaction, consistent product quality, and strong company culture. By putting people first, we address both social and economic sustainability.
How can Americo help make manufacturing more sustainable?
Safe and sustainable alternatives to hazardous chemicals
Safety and sustainability often go hand-in-hand. Safer and more convenient to handle chemicals are easier to use and dispose of properly. No employee wants to risk life and limb dealing with harsh chemicals if an alternative is available. In this way, safe chemistry contributes to social and economic sustainability, as reducing the risk threshold in your facility may increase worker satisfaction and employee retention.
Safer or less polluting alternatives sometimes carry a reputation for lesser efficacy or higher costs. While this may be true in some cases, customization and process adjustments can often mitigate these concerns. A consultation with our team may uncover safer options that don’t hamper your productivity or eat into your margins.
Phosphate discharge monitoring and management
While not all municipalities and regions have the same stringent requirements concerning phosphate discharge, it’s become a focus area for wastewater management.
When discharged, phosphates add phosphorus to the local environment. Phosphorus is an important building block for plant life, often acting as a limiting factor in plant growth rate—hence the use of phosphorus-based fertilizer in agriculture.
This becomes a problem when waterways become oversaturated with phosphorus. Disruptive and even deadly algae blooms can occur as a result. These explosions in algal growth result in “dead zones” where oxygen levels drop too low to sustain fish and other aquatic lifeforms. They can clog drains and other infrastructure, ruin recreational areas, and generate noxious odors.
As a result of these challenges, more and more local and state governments demand strict limits on the amount of phosphorus discharged from facilities of all types. We help manufacturers upgrade their wastewater management process, using precipitants, physical filtration, and other methods to reduce wastewater complexity before discharge. This not only protects local environments; there are significant cost-savings associated with decreasing the complexity of your industrial waste in the form of reduced disposal fees and less risk of fines.
Bath life optimization
Another way we assist companies in reducing their environmental footprint is by reducing their overall waste output. Many manufacturing processes rely on chemical baths. These baths may require frequent changeover for a variety of reasons: sludge formation, depletion of reactive chemicals, or other forms of contamination.
In many cases, we can increase the so-called “bath life” of your process. That may mean advanced filtration techniques, the use of coagulants or clumping agents to make sludge and debris removal easier, or the introduction of additives that prolong the reactive life of your baths.
By reducing bath changeovers through superior technology, your facility can squeeze more out of every dollar spent on process chemicals while lowering your waste output.
Counterflow/chemical & heat capture
While waste is inevitable in manufacturing, there are ways to recapture a great deal of otherwise lost heat with the right planning and setup. In this way, companies can effectively “double dip” on some of their resources, reducing their overall consumption.
A counterflow setup exposes hot process water to cool intake water (or vice versa, depending on the process) in an efficient way, facilitating highly efficient heat transfer. By configuring a counterflow setup instead of a parallel setup, we can help facilities achieve significant utility bill savings by reducing heat waste.
Equipment rehabilitation
In many cases, newer equipment offers greater efficiency, including better water and energy efficiency that results in better sustainability. However, equipment changeovers are expensive, disruptive, and have a “pay-back period” before their up-front environmental footprint gets outweighed by more efficient operation. Consider the environmental footprint of an electric vehicle. Replacing a gas-powered car with an EV is a good long-term strategy to reduce emissions, but it may take thousands of miles of driving before the EV “breaks even” versus maintaining the older gas vehicle.
With these practical considerations in mind, rehabilitating equipment can improve its efficiency and extend its life, allowing facilities to budget for an upgrade on a schedule that works for them. By providing a longer runway for companies to upgrade their equipment, we can help make the transition to sustainable technology easier and more affordable.
Conclusion: a path to sustainability for every manufacturer
Whether due to a desire for cost-savings, out of a need to avoid costly fines and disposal fees, or stemming from a genuine personal commitment to sustainability, there are strong business cases for any manufacturer to consider optimizing their chemical processes.
On whatever scale you plan to improve your manufacturing sustainability, Americo Chemical is a valuable and experienced partner. Interested in learning more? Contact us today to schedule a free consultation.
Want more insights like this?
Sign up for our newsletter and be the first to get the goods. Dive deeper into the world of chemical innovation and industry trends by signing up for our newsletter today!
You may also be interested in:
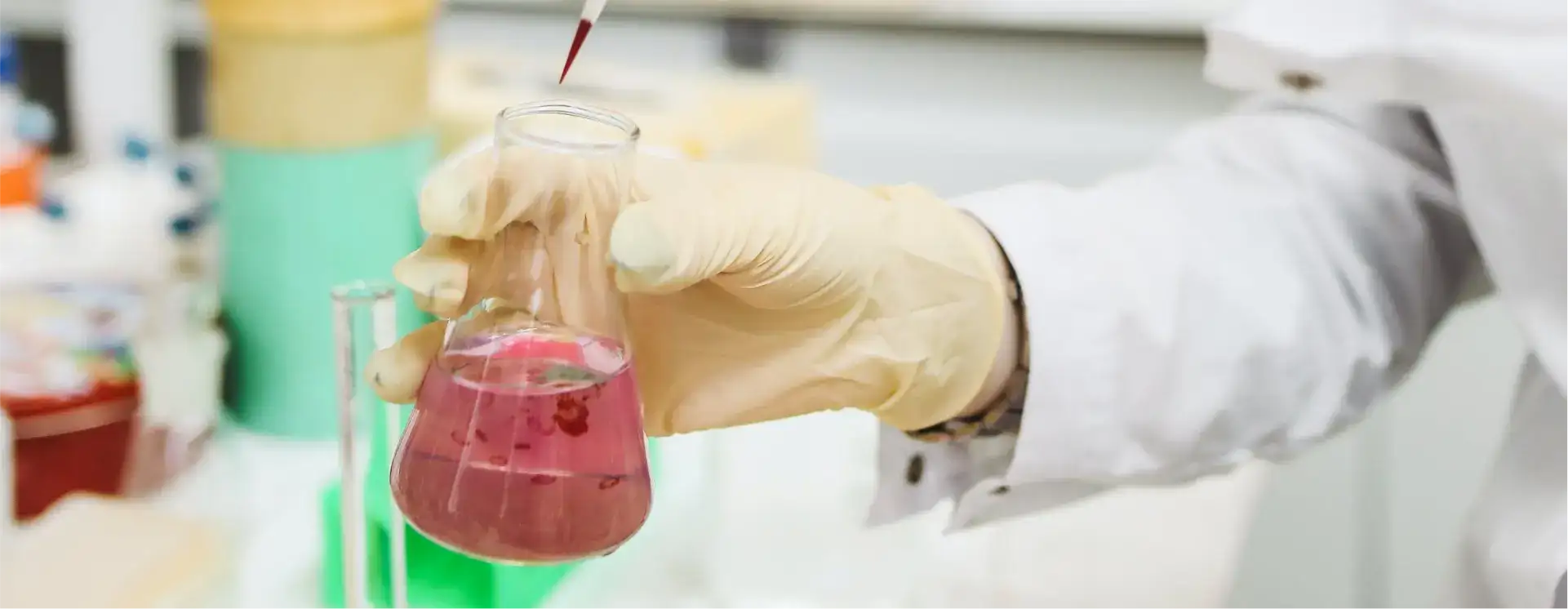
Ready to Get Started?
Value-focused customization is at the core of what we do. Our custom-engineered chemicals are tailored to the unique needs of each facility and process. This high level of customization allows Americo products to consistently outperform generic solutions from leading competitors.