IoT and Custom Chemicals: How Smart Sensors Enable Better Manufacturing Outcomes
IoT (Internet of Things) is the name given to a wide range of network-connected devices found in businesses and homes across America. While some people think of things like smart light bulbs and dishwashers when they hear IoT, there are many industrial applications for this networked technology.
IoT “smart sensors” are increasingly common in manufacturing facilities, allowing manufacturers to monitor processes and make data-driven decisions to optimize performance. Smart sensors enable superior quality management by feeding accurate live data back to dashboards and user interfaces. Quality management teams use this info to continually adjust and improve manufacturing performance, efficiency, and ROI.
Today we’ll look at IoT, smart sensors, and their relationship to the custom chemical solutions we specialize in at Americo Chemical.
Understanding smart sensor technology
Smart sensors do a lot more than their name may suggest. Sensing conditions like liquid levels or pH is just the first step. Smart sensors collect analog data much like any conventional sensor. Then, they digitize that data—turn it into a value that can be transmitted. This data gets sent to other devices, usually including a centralized computer system, via a wired or wireless connection. Today’s advanced sensors use Wi-Fi, Bluetooth, or custom wireless protocols to secure deliver data throughout your facility and beyond.
Types of smart sensors
There are as many types of smart sensors as there are types of data to collect. Let’s look at some of the top types of smart sensors found in manufacturing facilities.
Pressure sensors
Many industrial processes rely on pneumatic and hydraulic systems where maintaining ideal operating pressure is critical. Pressure sensors use a variety of methods to accurately monitor pressure levels. Many pressure sensors use a diaphragm that flexes or deforms based on pressure levels. The diaphragm’s level of deformation impacts the resistance or capacitance of an electrical component. The degree of impact on this electrical component corresponds to pressure levels in the measured vessel.
Temperature sensors
Temperature and pressures are two peas in a pod as they directly correlate to each other. Temperature sensors use a wide range of sensing techniques including purely analog options like bimetallic coils and electrical options like resistance temperature detection, where a metallic component’s electric resistance fluctuates based on temperature.
pH sensors
Maintaining appropriate pH is crucial for manufacturing, particularly for metal treatments and coatings. What most pH sensors actually detect is the presence of hydrogen ions. The concentration of hydrogen ions in a substance directly corresponds to its acidity. Using special glass electrodes that develop electrical potential under exposure to hydrogen ions, pH sensors compare the exposed electrode’s potential to a control electrode, deriving a pH value from the resulting difference.
Conductivity sensors
Detecting the conductivity of a liquid can determine the presence and levels of dissolved salts and other solids. This is particularly important in industrial wastewater management as dissolved salts contribute to the complexity—and by extension, the cost of disposal—of wastewater.
To calculate conductivity, two electrodes are submerged in a liquid. A current runs through them. The resistance between the electrodes determines the conductivity level, which in turn informs the level of dissolved solids in the measured material.
Level sensors
Maintaining appropriate levels in tanks can reduce wear and tear on equipment and prevent damage to cutting tools and manufactured products. Level sensors can work on a number of different principles, from physically detecting the presence of materials at a certain point in the tank to using ultrasonic sound waves to accurate measure even foamy or frothy tanks.
Flow sensors
Flow sensors measure the rate of flow of fluids including gases. The simplest method of measurement is to install a turbine or propeller in the pipe or vessel. This measures flow rate mechanically by measuring the speed of the turbine, like a water wheel in a river.
Other methods rely on more complex calculations that calculate flow rate based on thermal mass, ultrasonic waves, or electromagnetic conductivity.
Smart sensors and quality management
Smart sensors facilitate quality engineering and quality management in many ways. First, they help to establish baseline performance. Before a process can be optimized, it must be fully understood. Smart sensors validate assumptions and provide clear and accurate data to operators. This means that performance improvements can be tracked and measured against a reliable baseline.
Smart sensors provide granular and timely data to track changes in performance over time. Once smart sensors are installed, the parameters of a process may be adjusted “on the fly” based on accurate data. Testing new methods, including new custom chemical solutions, can be done quickly and with less risk as smart sensors provide immediate feedback.
How sensor data informs product quality
The relationship between the temperature of a fluid or the liquid level in a tank and the quality of an end product may not seem clear. Consider the application of a durable coating to a metal part. The quality of that coating may hinge on curing at a specific temperature. If a facility found their curing temperature fluctuated too much based on heating or cooling effects from nearby processes, they could take steps to address temperature fluctuation, thus improving product quality.
Lower than expected liquid levels in a tank of metalworking fluid could result in uneven flow rate, poor cut quality, or expedited equipment failure, all of which can impact both quality and process efficiency. Though these industrial metrics can sometimes seem abstract, their impact on a company’s bottom line can be significant.
Customized products through data analysis
At Americo Chemical, we rely on sensor data to enable our Total Systems Approach. By understanding the exact nature of your chemical challenges, we’re able to formulate chemistry that enhances your process.
In some cases, upgrading equipment to address minor mechanical issues like inconsistent flow rate or excess foaming in tanks can be prohibitively difficult or expensive. This is a case where a custom chemical solution—perhaps one with lower viscosity to improve flow rate, or with anti-foaming properties—can maintain product quality at a low cost while preparing for the significant capital expenditure of an equipment upgrade or replacement.
Enhanced safety through IoT
Safety in manufacturing should be top-of-mind for any facility. Safety facilitates better profitability through reduced legal risk and less time paid time off for workers due to illness or injury. Safe facilities have fewer production stoppages, improving output and lead times.
Industrial IoT including smart sensors can enhance safety for workers in a variety of ways.
Conventional sensors require workers to check and record their data periodically. This can involve climbing ladders, exposing workers to potentially harmful chemicals, or otherwise putting them in situations with elevated risk factors. IoT sensors can broadcast their data to workers remotely, greatly reducing the number of manual checks required.
Many smart sensors work in tandem with other automation solutions. A smart sensor can be connected to a valve, automatically shutting down a process if the temperature or pressure goes beyond safe limits. It can then log and report the incident, including information on conditions leading up to the incident. This kind of reporting can help facility managers understand points of failure and address challenges before they pose safety threats to workers.
Future trends in industrial IoT
AI and machine learning
Recent advancements in AI prove promising for industrial IoT. While human analysis is an important component of quality management and process engineering, AI and humans working together may result in even better outcomes. Machine learning models can suggest improvements that humans may miss or never even consider.
AI can also make data insights more accessible to more people. Instead of needing a data science background to interpret results, an AI interface might allow a facility manager to ask questions in plain English, receiving digestible insights from a chatbot.
“Digital twins”
Consider a manufacturing process from the point of view of a smart sensor system. It’s a consistent series of actions where various metrics must fall within acceptable ranges. Given enough historic and live data, data experts can create “digital twins” of manufacturing facilities. These are sophisticated digital models of manufacturing processes that can be used to test theoretical changes to the system without impacting production.
A digital twin is a safe sandbox to test ideas. Alternate chemicals with different physical properties can be programmed into the digital twin’s model to see how the new chemicals may impact the process. If the change results in improved metrics in the digital twin, it can be introduced to the real-world facility. Sensors report results from the real-world test back to the model. If the model’s proposed results prove inaccurate, it can be updated and improved based on live data. This cycle of continual improvement ensures the digital twin accurately represents the facility it’s modeled after.
Digital twins can also be used to train new staff on facility operations in a safe way. When combined with AI tools, digital twins may be able to recommend improvements to facility operations without human input.
Conclusion
In the dynamic landscape of industrial manufacturing, the integration of IoT and smart sensors has proven to be a game-changer, particularly in the realm of quality management. By harnessing the power of these technologies, Americo Chemical can offer customized solutions that enhance production efficiency and ensure the highest standards of product quality. Our commitment to leveraging cutting-edge sensor data not only optimizes processes but also paves the way for innovative approaches to chemical challenges. Whether you’re looking to refine existing operations or explore the possibilities of advanced IoT applications, we invite you to connect with us. Discover how our Total Systems Approach can transform your manufacturing outcomes, optimizing your operations for the future.
Want more insights like this?
Sign up for our newsletter and be the first to get the goods. Dive deeper into the world of chemical innovation and industry trends by signing up for our newsletter today!
You may also be interested in:
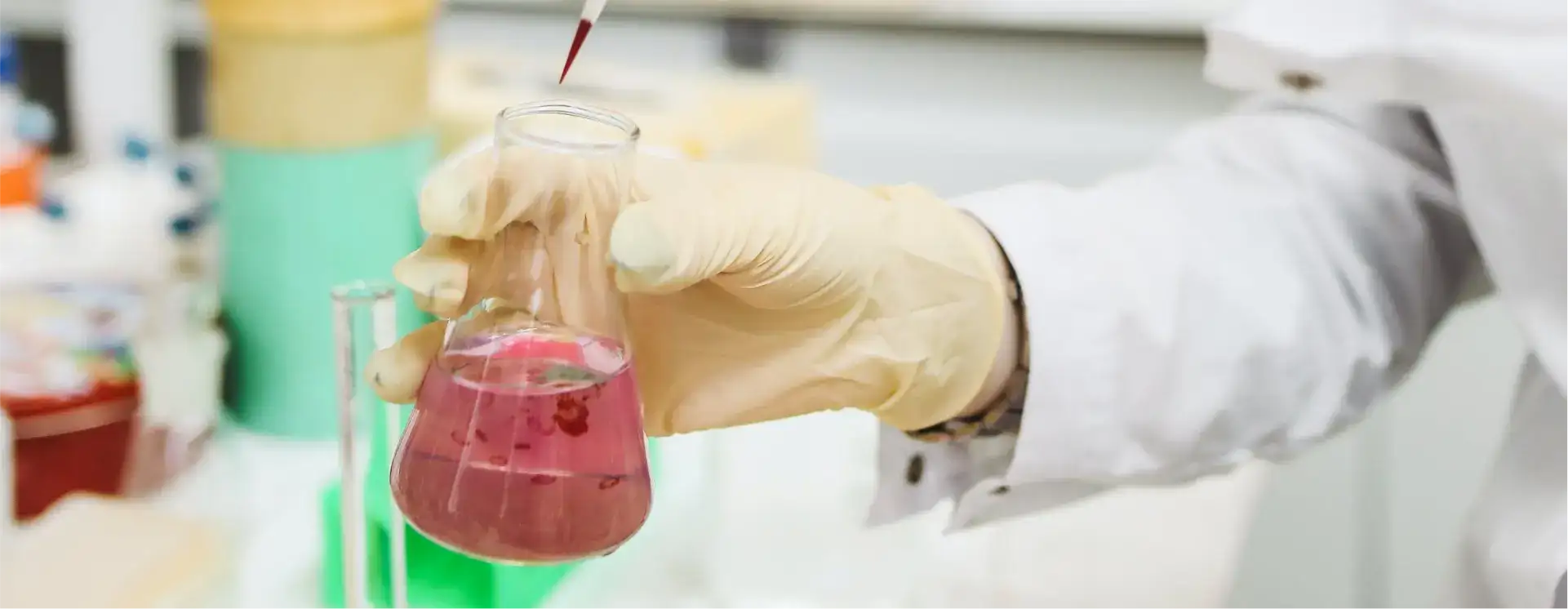
Ready to Get Started?
Value-focused customization is at the core of what we do. Our custom-engineered chemicals are tailored to the unique needs of each facility and process. This high level of customization allows Americo products to consistently outperform generic solutions from leading competitors.