Enhancing Efficiency with Just-In-Time Chemical Blending and Delivery
Introduction
Just-in-Time (JIT) manufacturing is a familiar concept to manufacturers of all kinds. Once known as the Toyota Production System due to its association with auto manufacturing techniques pioneered by Toyota, it’s now common practice across manufacturing sectors.
JIT aims to increase efficiency while reducing waste by producing and receiving goods only as they are needed. A more traditional manufacturing process relies on keeping large quantities of materials on-hand. This increases the physical footprint of manufacturing facilities while introducing risks like spoilage issues, material obsolescence, and inefficient resource management.
Though JIT has its own challenges—we all experienced supply chain disruptions during COVID that material warehousing at scale may have mitigated in some cases—it’s considered an efficient and effective best practice in many manufacturing scenarios.
Americo Chemical produces our custom solutions through a JIT model. This article will explain how JIT chemical supply works and why we believe it’s the best way to provide leading chemical solutions to manufacturers of all kinds.
Conventional chemical production vs. JIT production
In conventional chemical production, large quantities of pre-blended chemicals are produced and stored until needed. There are some natural benefits to this system: keeping materials on-hand can increase supply chain resiliency in some cases. Certain chemical production processes benefit from economies of scale, meaning that mass production and storage can be cheaper, at least in terms of up-front costs.
There are scenarios where conventional chemical production isn’t cost-efficient. Consider the added cost of storage, both for chemical suppliers and the customers they serve. Having months or years of supply at hand may seem like a good idea, but what if regulations change and your materials are no longer legal to use? What if your process chemicals experience spoilage over time, resulting in degraded performance or high amounts of waste?
A JIT production model blends a smaller quantity of chemicals to specification on an order-by-order basis. Provided the production process is efficient and the logistics system is resilient, this can result in decreased storage fees, less waste, and more possibilities to customize products.
Our quality management emphasis prioritizes continual process improvement. We work with manufacturers to identify and test chemical solutions to their biggest manufacturing challenges. This technique is most effective in a JIT system, where adjustments can be made per order until the highest-performance formulation is identified.
JIT chemical supply breakdown: how JIT works in the chemical sector
The following is an example JIT process in the chemical sector. Note the ability to collect feedback for continual performance improvements, something that is difficult to do under a conventional bulk supply model:
- Demand Forecasting and Inventory Management
- Analyze customer production data to predict chemical needs.
- Maintain minimal raw material inventory, relying on a network of suppliers for quick procurement.
- Production Planning and Chemical Blending
- Schedule blending operations to align closely with customer demand and delivery schedules.
- Use automated systems for precise mixing and blending to meet customer specifications.
- Quality Control and Packaging
- Conduct quality checks to ensure products meet standards.
- Package chemicals safely and label with clear handling instructions.
- Logistics and Delivery
- Organize logistics to ensure timely deliveries, aligning them with customer production needs.
- Use real-time tracking technologies to monitor shipments and adjust logistics as necessary.
- Customer Integration and Feedback
- Deliver chemicals directly to customer’s production lines or specified areas.
- Collect feedback to refine the process and implement continuous improvements.
Core benefits of JIT chemical blending and delivery
Reduced Waste
By delivering exact quantities of materials on a consistent schedule, JIT production reduces the potential for waste. Whether through spoilage, obsolescence, mismanagement, or other issues, conventional production tends to be more wasteful. There’s a psychological component to waste, as well. Companies that draw materials from enormous reserves may be less lean in general; their workers may perceive the reserves as effectively endless, prompting them to be less careful about waste and inefficient use. It may also be harder to monitor and control material usage if the reserves are particularly large and monitoring systems are not enforced.
Cost efficiency
While JIT may forgo the economies of scale typical of mass production, which can reduce unit costs by producing large quantities of goods at once, it can still be highly cost-effective for customers. By delivering materials and products precisely when they are needed, JIT minimizes the costs associated with holding and managing inventory. JIT enhances operational efficiency by reducing waste and freeing up capital that would otherwise be tied up in excess inventory. This allows companies to allocate resources more strategically, investing in innovation or quality improvements that can lead to better products and services.
Customization and Flexibility
Just-in-Time production significantly enhances customization and flexibility in the chemical sector, allowing companies to tailor chemical blends to precise customer specifications on demand. JIT minimizes the need for large inventories, enabling manufacturers to quickly adapt to changes in market demands or regulatory shifts without the burden of excess stock. This flexibility not only reduces waste and storage costs but also allows chemical producers to rapidly incorporate new formulations or adjust existing ones, maintaining competitiveness and responsiveness in a dynamic market environment.
Conclusion
Just-in-Time production offers transformative benefits for the chemical sector by enhancing efficiency, reducing waste, and providing significant flexibility and customization capabilities. By aligning chemical production and delivery with the exact timing and specifications of customer demand, JIT minimizes the need for large inventories, thereby cutting storage costs and reducing risks associated with chemical spoilage and obsolescence. This approach not only supports better resource management and cost savings but also enables chemical manufacturers to swiftly adapt to industry changes and customer needs. Consequently, JIT helps chemical companies maintain a competitive edge, ensure high quality and compliance, and sustain customer satisfaction through tailored products and responsive service.
Americo Chemical provides JIT solutions to a wide spectrum of manufacturing facilities. Specializing in metal treatments and pretreatments, coatings, process chemicals, and wastewater management chemistry, we’re available to help you optimize your chemical inputs.
Want more insights like this?
Sign up for our newsletter and be the first to get the goods. Dive deeper into the world of chemical innovation and industry trends by signing up for our newsletter today!
You may also be interested in:
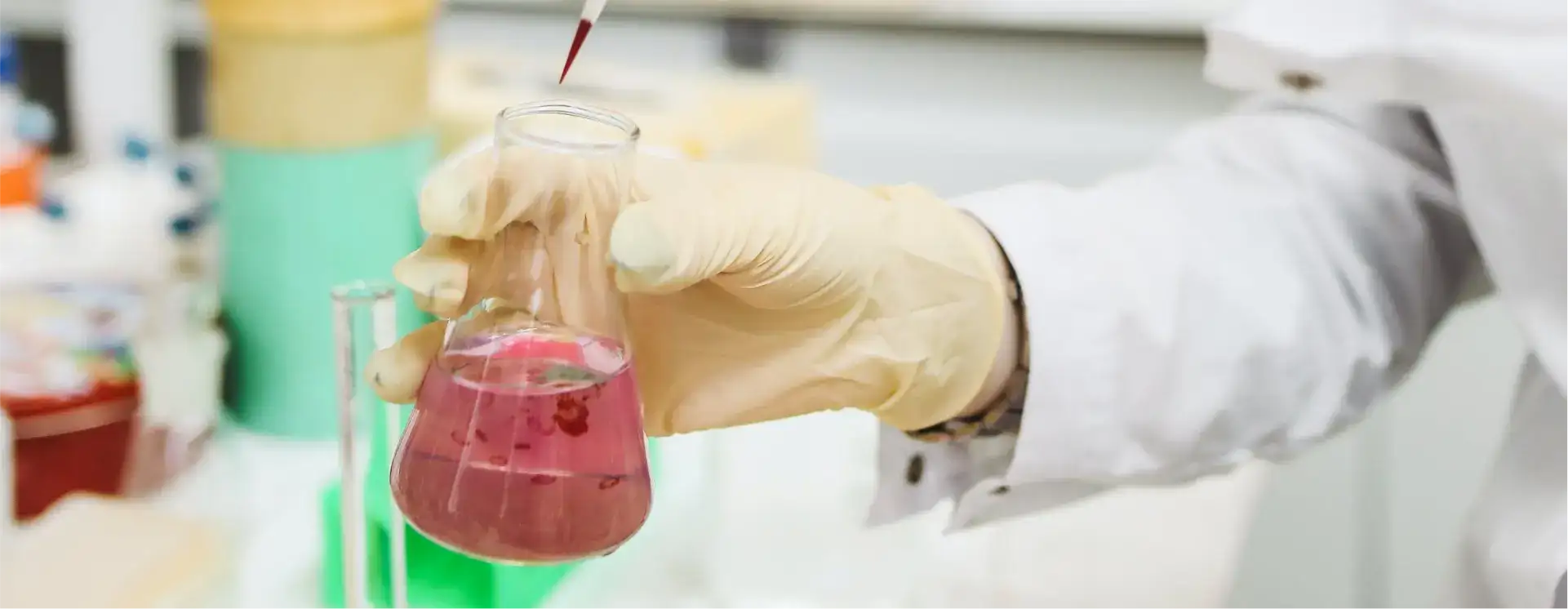
Ready to Get Started?
Value-focused customization is at the core of what we do. Our custom-engineered chemicals are tailored to the unique needs of each facility and process. This high level of customization allows Americo products to consistently outperform generic solutions from leading competitors.